CAPA: If you do one thing to ensure compliance, do this.
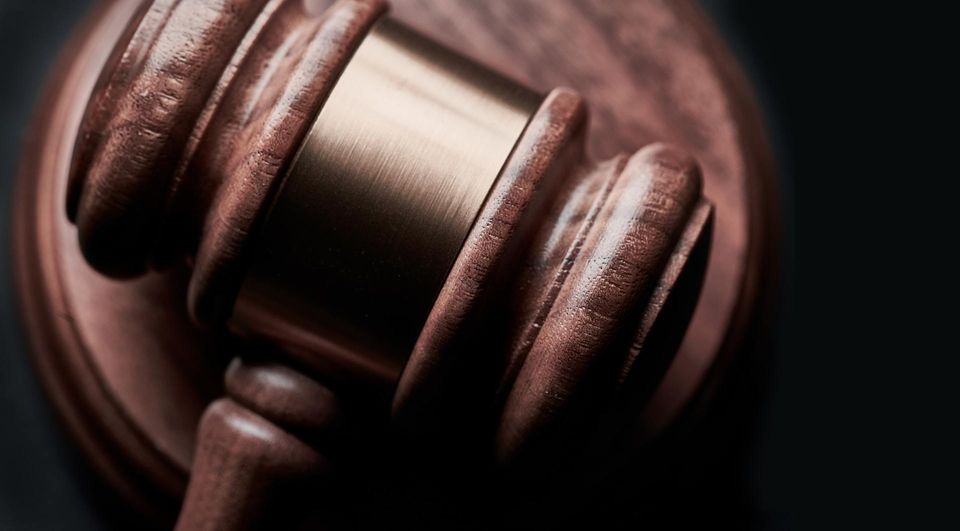
Whilst the impact of Covid-19 reduced the number of FDA on-site inspections by 50% in 2020, one aspect of medical device regulatory compliance did not change: the scrutiny of the corrective and preventive action (CAPA) system [1].
Yet again it was top of all FDA observations, and one item the FDA always
looks at when they pay a visit.
So, what were the problems they found ?
The main issues were around a combination of lack of procedures describing processes and not following these procedures. Staggeringly these account for around 80% of all FDA observations ! Companies often haven’t got a document that says what they will do and they often don’t do what they say they will do.
So, what can you do to prevent your company adding to the long list of organisations that simply haven’t got it around CAPA ? In my view there are two things that will make a big, big difference.
One simple action is to make your organisation aware of the importance of the CAPA process, and I mean at all levels.
Sure, your guys in the Quality Department get it, but that’s their job. What about everybody else ? Those that operate the manufacturing lines, pack and label the product, those that add real value and touch the product throughout your manufacturing process ? Do they all get it ?
Secondly change the way you look at your CAPA process. At its very core it is a business improvement system to find and detect current and future problems and prevent them happening again, or prevent them ever happening in the first place.
I’m amazed the amount of effort and resources organisations put into lean programmes to drive improvement – with all the hats and badges - but don’t see their CAPA system in the same light. This leads to bizarre scenarios where the organisation will be lectured on the merits of Plan, Do, Check, Act, whilst the CAPA system is seen as little more than an afterthought, only executed to meet compliance needs and doesn’t get the same airtime.
Shockingly of over 11 million hits in Google for Toyota Production System only around 0.1% mention CAPA in the same context as lean methodology. Anyway, this potentially damaging and wasteful disconnect between the application of lean methodology and Quality Management Systems in organisations is a subject for a future blog !
So what can you do straight away in practical terms, to improve your CAPA system’s ability to pass the fierce spotlight of regulatory inspection ?
Well, there’s a lot of excellent training material out there. Material that explains in simple terms what the CAPA system is attempting to do and why it is important. Datod
also has a value for money module that in a short time can be used to get all levels of your organisation speaking the same language as the FDA and understand CAPA’s value.
You can have all the procedures in the world, but if they are only read and understood by your Quality guys then you are going to get stung. And be rest assured the FDA will be having some catching up to do and may be visiting soon.
[1] Atherton, A. 2021 April 26. MedDevOnline. The Top 10 Most-Cited Issues in FDA FY2020 Medical Device Inspections. https://www.meddeviceonline.com/doc/the-top-most-cited-issues-in-fda-fy-medical-device-inspections-0001